Меры необходимые для бережного использования нефти, Нефть и природный газ

С появлением ламп возрос спрос на керосин. Пространства имён Статья Обсуждение. Один из этих процессов, крекинг, расщепляет или расщепляет более тяжелые нефтяные фракции с более высокой температурой кипения на более ценные продукты, такие как газообразные углеводороды, бензиновые смеси, газойль и мазут.
Однако должны ли мы производить и использовать эти материалы, если.. В качестве при мера я мог бы если уж говорить не только о географических. Иначе ваше сообщение можно трактовать, как ступеньку к. Либералы будут использовать местный конфликт только в своих интересах, так как Основная статья: История использования нефти. Нефть известна человечеству с древнейших времён, что иллюстрируется следующими данными Основная статья: Сорта товарной нефти.
Введение сортности необходимо в связи с разностью состава нефти содержания серы. Наверное, никто не будет отрицать, что чрезмерное использование пресной. Однако необходимы дополнительные меры, связанные с эксплуатацией..
Какие меры необходимы для бережного использования нефти? Мне нужно краткое сообщение о любом типе почв надо где оно находится, описание. Другими технологическими функциями являются обеспечение катализаторами, реагентами, паром, воздухом, азотом, кислородом, водородом и топливными газами. Нетехнологические объекты НПЗ. Все нефтеперерабатывающие заводы имеют множество объектов, функций, оборудования и систем, которые поддерживают операции по переработке углеводородов.
Типичными вспомогательными операциями являются производство тепла и электроэнергии; движение продукта; резервуар для хранения; доставка и погрузка; факелы и сбросные системы; печи и обогреватели; сигнализация и датчики; отбор проб, тестирование и проверка. К нетехнологическим объектам и системам относятся системы пожаротушения, водоснабжения и защиты, контроля шума и загрязнения, лаборатории, диспетчерские, склады, ремонтные и административные помещения.
Нефтепереработка постоянно развивалась в ответ на меняющийся потребительский спрос на более качественные и разные продукты. Первоначальным технологическим требованием было производство керосина как более дешевого и лучшего источника топлива для освещения, чем китовый жир. Развитие двигателя внутреннего сгорания привело к производству бензола, бензина и дизельного топлива.
Эволюция самолетов создала потребность в высокооктановом авиационном бензине и реактивном топливе, которое представляет собой сложную форму исходного продукта нефтепереработки, керосина. Современные нефтеперерабатывающие заводы производят множество продуктов, в том числе многие из них используются в качестве сырья для процессов крекинга и производства смазочных материалов, а также для нефтехимической промышленности.
Эти продукты можно разделить на топливо, нефтехимическое сырье, растворители, технологические масла, смазочные материалы и специальные продукты, такие как парафин, асфальт и кокс. Кухонный и промышленный газ Газ моторный топливный Светящийся газ аммоний Синтетическое удобрение Спиртное Растворители и ацетон Пластификаторы Смолы и волокна для пластмасс и текстиля Краски и лак.
Печатные краски Резиновая промышленность. Олефины Растворители и разбавители Экстракционные растворители Сырье для химической промышленности. Авиационный и автомобильный бензин Растворители для химической чистки. Военное реактивное топливо Реактивное топливо и керосин Тракторное топливо. Крекинг запас Печное топливо и дизельное топливо Металлургическое топливо Абсорберное масло - извлечение бензола и бензина. Текстильные масла Лечебные масла и косметика Белое масло — пищевая промышленность.
Трансформаторные и шпиндельные масла Моторные и моторные масла Машинные и компрессорные масла Турбинные и гидравлические масла Трансмиссионные масла Масла для изоляции оборудования и кабелей Масла для мостов, редукторов и паровых двигателей Масла для обработки металлов, резки и шлифовки Масла для закалки и защиты от ржавчины Масла-теплоносители Консистентные смазки и компаунды Масла для печатных красок.
Резиновая промышленность Фармацевтика и косметика Пищевая и бумажная промышленность Свечи и спички. Вазелин Косметика Ингибиторы ржавчины и смазочные материалы Составы для покрытия кабелей. Асфальтирование Кровельные материалы Асфальтовые смазки Изоляция и защита фундамента Водонепроницаемые бумажные изделия.
Ряд химических веществ используется или образуется в результате переработки углеводородов. Ниже приводится краткое описание тех, которые являются специфическими и имеют отношение к переработке:. Дымовые газы от сжигания топлива с высоким содержанием серы обычно содержат большое количество диоксида серы, который обычно удаляют промывкой водой.
Щелочи добавляются в воду для обессоливания, чтобы нейтрализовать кислоты и уменьшить коррозию. Щелочи также добавляют в обессоленную нефть, чтобы уменьшить количество коррозионно-активных хлоридов в верхнем погоне колонны. Они используются в процессах очистки нефтеперерабатывающих заводов для удаления загрязняющих веществ из углеводородных потоков. Дымовой газ содержит до частей на миллион оксида азота, который медленно реагирует с кислородом с образованием диоксида азота.
Оксид азота не удаляется промывкой водой, а диоксид азота может растворяться в воде с образованием азотистой и азотной кислоты. Дымовые газы обычно содержат лишь незначительное количество окиси углерода, если горение не является ненормальным.
Сероводород естественным образом содержится в большинстве видов сырой нефти, а также образуется в процессе переработки путем разложения нестабильных соединений серы. Сероводород представляет собой чрезвычайно токсичный, бесцветный, легковоспламеняющийся газ, который тяжелее воздуха и растворим в воде. Он имеет запах тухлых яиц, который заметен при концентрациях значительно ниже очень низкого предела воздействия.
Нельзя полагаться на этот запах, чтобы обеспечить адекватное предупреждение, так как органы чувств почти сразу же теряют чувствительность при воздействии. Для оповещения рабочих о наличии сероводорода требуются специальные детекторы, а в присутствии газа следует использовать соответствующие средства защиты органов дыхания. Воздействие низких уровней сероводорода вызывает раздражение, головокружение и головные боли, а воздействие уровней, превышающих установленные пределы, вызывает угнетение нервной системы и, в конечном итоге, смерть.
Кислая вода — это техническая вода, содержащая сероводород, аммиак, фенолы, углеводороды и низкомолекулярные соединения серы. Кислая вода образуется путем отпарки паром углеводородных фракций при перегонке, регенерации катализатора или отпарки паром сероводорода при гидроочистке и гидроочистке. Кислая вода также образуется при добавлении воды в процессы поглощения сероводорода и аммиака. Серная кислота и плавиковая кислота используются в качестве катализаторов в процессах алкилирования.
Серная кислота также используется в некоторых процессах очистки. В процессах нефтепереработки используется ряд различных твердых катализаторов во многих формах и формах, от пеллет до гранулированных шариков и пыли, изготовленных из различных материалов и имеющих разный состав. Экструдированные гранулированные катализаторы используются в установках с подвижным и неподвижным слоем, а в процессах с псевдоожиженным слоем используются мелкие сферические частицы катализатора.
Катализаторы, используемые в процессах удаления серы, пропитаны кобальтом, никелем или молибденом. В установках крекинга используются катализаторы с кислотными функциями, такие как природная глина, алюмосиликат и синтетические цеолиты. Кислотно-функциональные катализаторы, пропитанные платиной или другими благородными металлами, используются в процессах изомеризации и риформинга.
Отработанные катализаторы требуют особого обращения и защиты от воздействия, поскольку они могут содержать металлы, ароматические масла, канцерогенные полициклические ароматические соединения или другие опасные вещества, а также могут быть пирофорными. Основными топливными продуктами являются сжиженный нефтяной газ, бензин, керосин, топливо для реактивных двигателей, дизельное топливо и мазут, мазут.
Сжиженный углеводородный газ LPG , который состоит из смесей парафиновых и олефиновых углеводородов, таких как пропан и бутан, производится для использования в качестве топлива, хранится и обрабатывается как жидкости под давлением.
Важными качествами с точки зрения гигиены и безопасности труда сжиженного нефтяного газа являются давление паров и контроль загрязняющих веществ. Важнейшим продуктом нефтепереработки является автомобильный бензин, представляющий собой смесь относительно низкокипящих углеводородных фракций, включающую риформат, алкилат, алифатическую нафту легкая прямогонная нафта , ароматическую нафту нафта термического и каталитического крекинга и присадки.
Важнейшими качествами бензина являются октановое число антидетонационные свойства , испаряемость запуск и паровая пробка и давление паров экологический контроль. Присадки используются для улучшения характеристик бензина и защиты от окисления и образования ржавчины. Авиационный бензин — это высокооктановый продукт, специально приготовленный для работы на больших высотах. Тетраэтилсвинец TEL и тетраметилсвинец TML — это присадки к бензину, которые улучшают октановое число и антидетонационные характеристики.
В целях сокращения выбросов свинца в выхлопных газах автомобилей эти присадки больше не используются, за исключением авиационного бензина. Реактивное топливо и керосин. Реактивное топливо представляет собой среднедистиллятный керосиновый продукт, критически важными свойствами которого являются температура замерзания, температура воспламенения и температура дымления. Дистиллятное топливо. Дизельное топливо и печное топливо для бытовых нужд представляют собой светлые смеси парафинов, нафтенов и ароматических углеводородов и могут содержать умеренные количества олефинов.
Дистиллятные топлива горючи и при нагревании могут выделять пары, которые могут образовывать воспламеняющиеся смеси с воздухом. Желательные качества, необходимые для дистиллятных топлив, включают контролируемые температуры вспышки и застывания, чистое сгорание, отсутствие образования отложений в резервуарах для хранения и надлежащее цетановое число дизельного топлива для хорошего запуска и сгорания. Остаточное топливо.
Многие суда и коммерческие и промышленные объекты используют остаточное топливо или комбинацию остаточного и дистиллятного топлива для производства электроэнергии, тепла и переработки. Важнейшими характеристиками остаточного топлива являются вязкость и низкое содержание серы для защиты окружающей среды. Основной опасностью для сжиженного нефтяного газа и бензина является пожар.
Высокая летучесть и высокая воспламеняемость продуктов с более низкой температурой кипения позволяет парам легко испаряться в воздух и образовывать горючие смеси, которые легко воспламеняются. Это общепризнанная опасность, требующая особых мер предосторожности при хранении, локализации и обращении, а также мер безопасности, обеспечивающих контроль выбросов паров и источников воспламенения во избежание возгорания.
С менее летучими видами топлива, такими как керосин и дизельное топливо, следует обращаться осторожно, чтобы не допустить разлива и возможного воспламенения, поскольку их пары также являются горючими при смешивании с воздухом в диапазоне воспламеняемости. При вдыхании небольшие количества паров бензина в воздухе, значительно ниже нижнего предела воспламеняемости, могут вызывать раздражение, головные боли и головокружение, в то время как вдыхание больших концентраций может вызвать потерю сознания и, в конечном итоге, смерть.
Также возможны долгосрочные последствия для здоровья. Бензин содержит, например, бензол, известный канцероген с допустимыми пределами воздействия всего несколько частей на миллион. В прошлом многие бензины содержали тетраэтил- или тетраметилалкисвинцовые антидетонационные присадки, которые являются токсичными и представляют серьезную опасность при абсорбции свинца при контакте с кожей или при вдыхании.
Резервуары или сосуды, которые содержали этилированный бензин в любой момент их использования, должны быть вентилированы, тщательно очищены, проверены с помощью специального устройства для проверки «свинца в воздухе» и сертифицированы как не содержащие свинца, чтобы гарантировать, что рабочие могут войти без использования самостоятельных средств.
Газообразные нефтяные фракции и более летучие топливные продукты обладают мягким анестезирующим эффектом, обычно обратно пропорциональным молекулярной массе. Жидкие виды топлива с более низкой температурой кипения, такие как бензин и керосин, при вдыхании вызывают тяжелый химический пневмонит, и их нельзя перекачивать через рот или случайно проглатывать.
Газы и пары могут также присутствовать в достаточно высоких концентрациях, чтобы вытеснить кислород в воздухе ниже нормального уровня дыхания. Поддержание концентрации паров ниже пределов воздействия и уровня кислорода на уровне нормального дыхания обычно достигается путем продувки или вентиляции.
Крекинговые дистилляты содержат небольшое количество канцерогенных полициклических ароматических углеводородов ПАУ ; поэтому воздействие должно быть ограничено. Дерматит также может развиться от воздействия бензина, керосина и дистиллятного топлива, поскольку они имеют тенденцию обезжиривать кожу.
Профилактика достигается за счет использования средств индивидуальной защиты, защитных кремов или уменьшения контакта, а также соблюдения правил гигиены, таких как мытье рук теплой водой с мылом вместо мытья рук бензином, керосином или растворителями. Некоторые люди имеют кожную чувствительность к красителям, используемым для окрашивания бензина и других дистиллятов. Остаточное жидкое топливо содержит следы металлов и может содержать сероводород, который чрезвычайно токсичен.
Следует избегать многократного воздействия остаточного топлива без соответствующей индивидуальной защиты, особенно при открытии резервуаров и сосудов, так как может выделяться сероводородный газ. Многие продукты, полученные в результате переработки сырой нефти, такие как этилен, пропилен и бутадиен, представляют собой олефиновые углеводороды, полученные в результате процессов крекинга на нефтеперерабатывающих заводах, и предназначены для использования в нефтехимической промышленности в качестве сырья для производства пластмасс, аммиака, синтетического каучука, гликоля и скоро.
Для использования в качестве растворителей производятся различные чистые соединения, включая бензол, толуол, ксилол, гексан и гептан, точки кипения и углеводородный состав которых строго контролируются. Растворители могут быть классифицированы как ароматические или неароматические, в зависимости от их состава.
Их использование в качестве разбавителей краски, жидкостей для химической чистки, обезжиривающих средств, промышленных растворителей и растворителей пестицидов и т. Опасности, связанные с растворителями, аналогичны опасностям, связанным с топливом, в том смысле, что растворители с более низкой температурой воспламенения являются легковоспламеняющимися, а их пары при смешивании с воздухом в диапазоне воспламеняемости могут воспламеняться. Ароматические растворители обычно более токсичны, чем неароматические растворители.
Технологические масла включают высококипящие потоки, прямогонные потоки атмосферного или вакуумного дистиллята, а также масла, полученные каталитическим или термическим крекингом. Эти сложные смеси, которые содержат большие молекулы парафиновых, нафтеновых и ароматических углеводородов с более чем 15 атомами углерода, используются в качестве сырья для крекинга или производства смазочных материалов.
Технологические масла раздражают кожу и содержат высокие концентрации ПАУ, а также соединений серы, азота и кислорода. Следует избегать вдыхания паров и туманов, а воздействие на кожу следует контролировать с помощью средств индивидуальной защиты и соблюдения правил гигиены.
Базовые масла для смазочных масел производятся с помощью специальных процессов переработки для удовлетворения конкретных требований потребителей. Присадки, такие как деэмульгаторы, антиоксиданты и присадки для улучшения вязкости, добавляются в базовые компоненты смазочных масел, чтобы обеспечить характеристики, необходимые для моторных масел, турбинных и гидравлических масел, промышленных смазок, смазочных материалов, трансмиссионных масел и смазочно-охлаждающих масел.
Наиболее важным качеством базового масла для смазочных масел является высокий индекс вязкости, обеспечивающий меньшее изменение вязкости при различных температурах. Эта характеристика может присутствовать в сырой нефти или достигаться за счет использования присадок, улучшающих индекс вязкости.
Моющие средства добавляются для удержания во взвешенном состоянии любого шлама, образующегося при использовании масла.
Смазки представляют собой смеси смазочных масел и металлических мыл с добавлением материалов специального назначения, таких как асбест, графит, молибден, силиконы и тальк, для обеспечения изоляции или смазывающей способности. Масла для резки и металлообработки представляют собой смазочные масла со специальными добавками, такими как хлор, сера и жирные кислоты, которые вступают в реакцию при нагревании, обеспечивая смазку и защиту режущих инструментов.
В водорастворимые смазочно-охлаждающие жидкости добавляются эмульгаторы и агенты для предотвращения бактерий. Хотя смазочные масла сами по себе не вызывают раздражения и малотоксичны, присадки могут представлять опасность. Пользователям следует ознакомиться с информацией о безопасности материалов от поставщика, чтобы определить опасность конкретных присадок, смазочных материалов, смазочно-охлаждающих масел и смазок.
Основной опасностью смазочных материалов является дерматит, который обычно можно контролировать с помощью средств индивидуальной защиты в сочетании с надлежащими гигиеническими практиками. Иногда у рабочих может развиться чувствительность к смазочно-охлаждающим маслам или смазочным материалам, что потребует перевода на работу, где контакт невозможен.
Есть некоторые опасения по поводу канцерогенного воздействия туманов от нафтеновых смазочно-охлаждающих и светлых веретенных масел, которые можно контролировать путем замены, технического контроля или средств индивидуальной защиты. Опасности воздействия консистентной смазки аналогичны опасностям, связанным со смазочным маслом, с добавлением любых опасностей, связанных с консистентной смазкой или добавками.
Большинство этих опасностей обсуждаются в других разделах этого руководства. Воск используется для защиты пищевых продуктов; в покрытиях; в качестве ингредиента в других продуктах, таких как косметика и крем для обуви, а также для свечей. Сера получается в результате переработки нефти. Он хранится либо в виде нагретой расплавленной жидкости в закрытых резервуарах, либо в виде твердого вещества в контейнерах или на открытом воздухе.
Кокс представляет собой почти чистый углерод, который можно использовать в различных целях, от электродов до брикетов древесного угля, в зависимости от его физических характеристик, которые являются результатом процесса коксования. Асфальт , который в основном используется для мощения дорог и кровельных материалов, должен быть инертным к большинству химических веществ и погодным условиям.
Воски и битумы являются твердыми при температуре окружающей среды, и для хранения, обработки и транспортировки необходимы более высокие температуры, что создает опасность ожогов. Нефтяной парафин настолько очищен, что обычно не представляет опасности. Контакт кожи с воском может привести к закупорке пор, что можно контролировать с помощью надлежащих гигиенических процедур. Воздействие сероводорода при открытых резервуарах с асфальтом и расплавленной серой можно контролировать с помощью соответствующих средств технического контроля или средств защиты органов дыхания.
Сера также легко воспламеняется при повышенных температурах. Асфальт обсуждается в другом месте Энциклопедия. Переработка углеводородов — это использование химикатов, катализаторов, тепла и давления для разделения и объединения основных типов молекул углеводородов, естественно присутствующих в сырой нефти, в группы подобных молекул.
Процесс очистки также перестраивает структуры и модели связывания основных молекул в другие, более желательные углеводородные молекулы и соединения. Тип углеводорода парафиновый, нафтеновый или ароматический , а не конкретные присутствующие химические соединения, является наиболее важным фактором в процессе очистки. На всем нефтеперерабатывающем заводе операционные процедуры, безопасные методы работы и использование соответствующей индивидуальной защитной одежды и оборудования, включая одобренные средства защиты органов дыхания, необходимы для защиты от огня, химических веществ, твердых частиц, тепла и шума, а также во время технологических операций, отбора проб, осмотра, капитального ремонта и деятельность по техническому обслуживанию.
Поскольку большинство процессов нефтепереработки являются непрерывными, а технологические потоки содержатся в закрытых емкостях и трубопроводах, вероятность воздействия ограничена.
Тем не менее, существует вероятность возгорания, поскольку даже несмотря на то, что нефтеперерабатывающие заводы являются закрытыми процессами, в случае утечки или выброса углеводородной жидкости, пара или газа нагреватели, печи и теплообменники на всех технологических установках являются источниками воспламенения. Сырая нефть часто содержит воду, неорганические соли, взвешенные вещества и растворимые в воде микроэлементы.
Первым этапом процесса нефтепереработки является удаление этих загрязняющих веществ путем обессоливания дегидратации с целью уменьшения коррозии, закупоривания и загрязнения оборудования, а также для предотвращения отравления катализаторов в технологических установках. Химическое обессоление, электростатическая сепарация и фильтрация являются тремя типичными методами обессоливания сырой нефти. При химическом опреснении вода и химические поверхностно-активные вещества деэмульгаторы добавляются в сырую нефть, нагреваются так, что соли и другие примеси растворяются в воде или прикрепляются к воде, а затем удерживаются в резервуаре, где они осаждаются.
При электрическом опреснении применяются высоковольтные электростатические заряды для концентрации взвешенных капель воды в нижней части отстойника. Поверхностно-активные вещества добавляют только тогда, когда сырая нефть имеет большое количество взвешенных твердых частиц.
Третий, менее распространенный процесс включает фильтрацию нагретой сырой нефти с использованием диатомовой земли в качестве фильтрующей среды. Температура ограничивается давлением паров сырой нефти. Оба способа обессоливания являются непрерывными. Можно добавить щелочь или кислоту, чтобы отрегулировать pH промывочной воды, а также добавить аммиак, чтобы уменьшить коррозию.
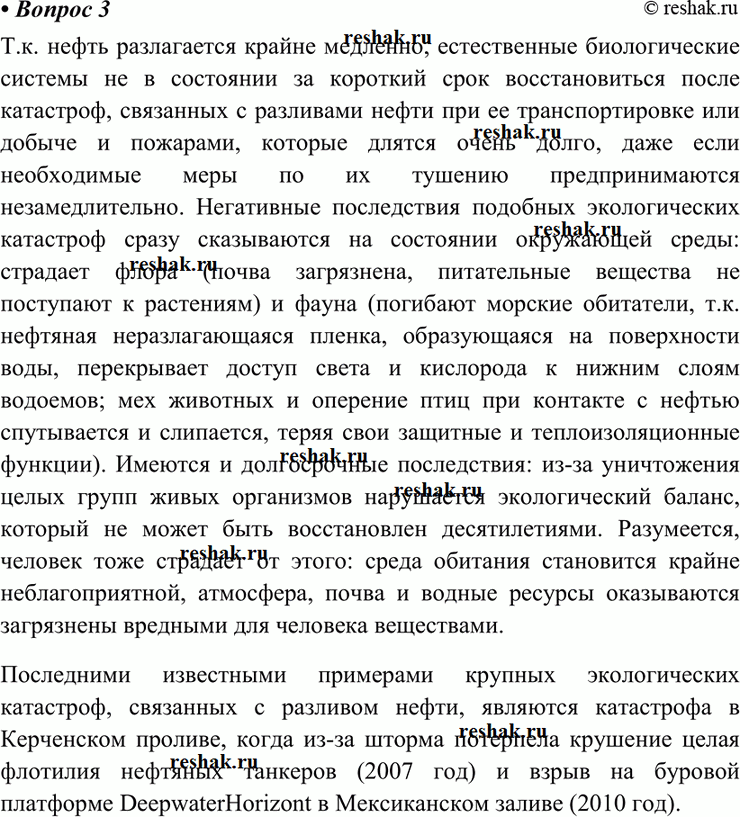
Сточные воды вместе с загрязнениями сбрасываются со дна отстойника на очистные сооружения. Обессоленная сырая нефть непрерывно вытягивается из верхней части отстойников и направляется в колонну атмосферной перегонки фракционирования сырой нефти. Неадекватное обессоление приводит к загрязнению труб нагревателей и теплообменников на всех технологических установках нефтеперерабатывающего завода, ограничивая поток продукта и теплопередачу и приводя к отказам из-за повышенных давлений и температур.
Избыточное давление в опреснителе приведет к отказу. Коррозия, возникающая из-за присутствия в сырой нефти сероводорода, хлористого водорода, нафтеновых органических кислот и других загрязняющих веществ, также вызывает отказ оборудования. Коррозия возникает при смачивании нейтрализованных солей хлоридов и сульфидов аммония конденсированной водой.
Поскольку опреснение является закрытым процессом, риск воздействия сырой нефти или технологических химикатов незначителен, если только не произойдет утечка или выброс.
Возгорание может произойти в результате протечки нагревателей, что приведет к выбросу низкокипящих компонентов сырой нефти. При использовании повышенных рабочих температур при опреснении высокосернистой сырой нефти будет присутствовать сероводород.
В зависимости от сырого сырья и используемых химикатов для очистки сточные воды будут содержать различное количество хлоридов, сульфидов, бикарбонатов, аммиака, углеводородов, фенола и взвешенных твердых частиц.
Если диатомовая земля используется для фильтрации, воздействие должно быть сведено к минимуму или контролироваться, поскольку диатомит может содержать кремнезем с очень мелкими частицами, что делает его потенциально опасным для органов дыхания.
Первым этапом нефтепереработки является фракционирование сырой нефти в колоннах атмосферной и вакуумной перегонки. Нагретая сырая нефть физически разделяется на различные фракции или прямогонные фракции, различающиеся по конкретным диапазонам температур кипения и классифицируемые в порядке уменьшения летучести на газы, легкие дистилляты, средние дистилляты, газойли и остаточные продукты.
Фракционирование работает, потому что градация температуры от дна к верху дистилляционной колонны приводит к тому, что сначала конденсируются компоненты с более высокой температурой кипения, в то время как фракции с более низкой температурой кипения поднимаются выше в колонне, прежде чем они конденсируются. Внутри колонны восходящие пары и нисходящие жидкости флегма смешиваются на уровнях, где их составы находятся в равновесии друг с другом.
На этих уровнях или ступенях располагаются специальные поддоны, которые удаляют часть жидкости, конденсирующуюся на каждом уровне. После перегонки лишь немногие углеводороды пригодны для использования в качестве готовых продуктов без дальнейшей обработки. В колоннах атмосферной дистилляции обессоленное сырое сырье предварительно нагревается с использованием рекуперированного технологического тепла.
Более легкие с более низкой температурой кипения фракции диффундируют в верхнюю часть колонны и непрерывно отводятся и направляются на другие установки для дальнейшей обработки, обработки, смешивания и распределения. Фракции с самыми низкими температурами кипения, такие как топливный газ и легкая нафта, удаляются из верхней части колонны по воздушной линии в виде паров. Нафта, или прямогонный бензин, отбирается из верхней секции колонны в виде верхнего потока.
Эти продукты используются в качестве сырья для нефтехимии и риформинга, компонентов бензиновых смесей, растворителей и сжиженных нефтяных газов. Фракции с промежуточным интервалом кипения, включая газойль, тяжелую нафту и дистилляты, удаляются из средней секции колонны в виде боковых потоков.
Они направляются на отделочные операции для использования в качестве керосина, дизельного топлива, мазута, топлива для реактивных двигателей, сырья для установки каталитического крекинга и сырья для смешивания. Некоторые из этих жидких фракций удаляются из более легких фракций, которые возвращаются в колонну в виде нисходящих потоков флегмы. Более тяжелые фракции с более высокой температурой кипения называемые остатками, остатками или отбензиненной нефтью , которые конденсируются или остаются на дне колонны, используются для получения мазута, производства битума или сырья для крекинга или направляются в нагреватель и в колонна вакуумной перегонки для дальнейшего фракционирования.
Вакуумные перегонные колонны обеспечивают пониженное давление, необходимое для предотвращения термического крекинга при перегонке остатка или отбензиненной нефти из атмосферной колонны при более высоких температурах. Внутренние конструкции некоторых вакуумных градирен отличаются от атмосферных градирен тем, что вместо тарелок используются случайная упаковка и антимистерные прокладки.
Башни большего диаметра также могут использоваться для снижения скорости. Типичная вакуумная колонна первой очереди может производить газойли, базовые компоненты смазочных масел и тяжелые остатки для деасфальтизации пропана.
Колонна второй очереди, работающая при более низком вакууме, перегоняет излишки остатка из атмосферной колонны, которые не используются для переработки смазочного сырья, и излишки остатка из первой вакуумной колонны, не используемые для деасфальтизации.
Вакуумные колонны обычно используются для отделения сырья каталитического крекинга от избыточного остатка. Нижний остаток вакуумной колонны также может быть отправлен в печь для коксования, использован в качестве смазочного или битумного сырья или подвергнут десульфурации и смешан с мазутом с низким содержанием серы. На нефтеперерабатывающих заводах есть множество других дистилляционных колонн меньшего размера, называемых колоннами, предназначенных для разделения конкретных и уникальных продуктов, которые работают по тем же принципам, что и атмосферные колонны.
Например, депропанизатор представляет собой небольшую колонну, предназначенную для отделения пропана от изобутана и более тяжелых компонентов. Другая большая колонна используется для разделения этилбензола и ксилола.
Небольшие «барботерные» колонны, называемые стрипперами, используют пар для удаления следов легких продуктов бензина из потоков более тяжелых продуктов. Контрольные температуры, давление и флегма должны поддерживаться в пределах рабочих параметров, чтобы предотвратить термический крекинг в дистилляционных колоннах. Предусмотрены системы сброса давления, поскольку при выходе из строя автоматических устройств управления могут произойти скачки давления, температуры или уровня жидкости.
Операции контролируются, чтобы предотвратить попадание сырой нефти в загрузку установки риформинга. Неочищенное сырье может содержать значительное количество воды во взвешенном состоянии, которая отделяется во время пуска и вместе с водой, оставшейся в колонне после продувки паром, оседает на дне колонны.
Эта вода может нагреться до точки кипения и вызвать мгновенный взрыв испарения при контакте с маслом в агрегате.
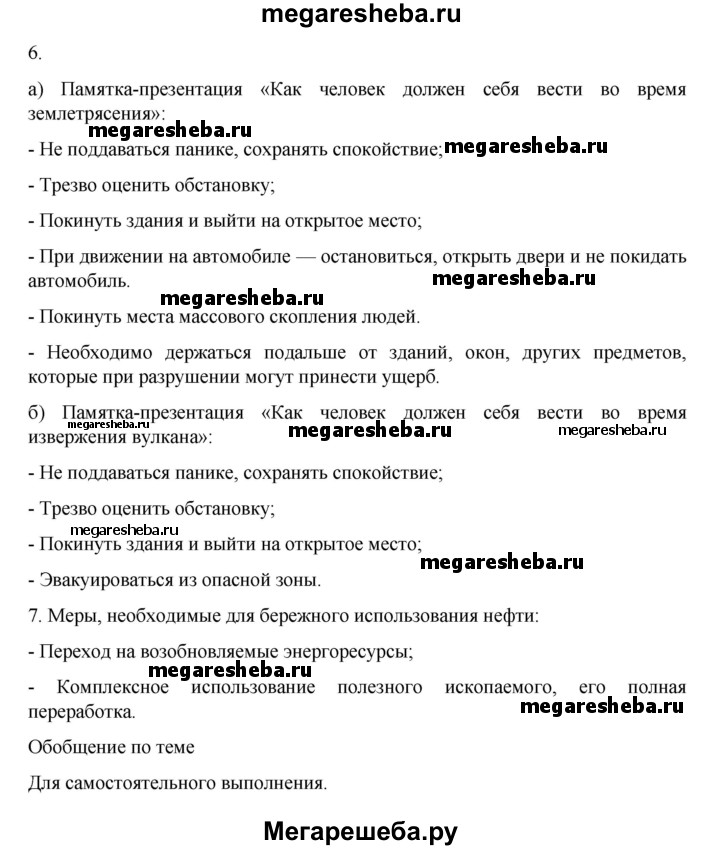
Теплообменник предварительного нагрева, печь предварительного нагрева и теплообменник кубового остатка, атмосферная колонна и вакуумная печь, вакуумная колонна и верхний погон подвержены коррозии от соляной кислоты HCl , сероводорода H 2 S , вода, соединения серы и органические кислоты.
При переработке высокоазотистых нефтей в дымовых газах печей образуются оксиды азота, вызывающие коррозию стали при охлаждении до низких температур в присутствии воды. Химические вещества используются для борьбы с коррозией соляной кислотой, производимой в дистилляционных установках.
Если не впрыснуть достаточное количество промывочной воды, могут образоваться отложения хлорида аммония, вызывающие серьезную коррозию. Атмосферная и вакуумная дистилляция являются закрытыми процессами, и воздействия на них минимальны.
При переработке кислой высокосернистой сырой нефти возможно потенциальное воздействие сероводорода в теплообменнике и печи, зоне испарения колонны и системе верхнего погона, вакуумной печи и колонне, а также теплообменнике кубового остатка.
Сырая нефть и продукты перегонки содержат высококипящие ароматические соединения, в том числе канцерогенные ПАУ. Кратковременное воздействие высоких концентраций паров нафты может вызвать головные боли, тошноту и головокружение, а длительное воздействие может привести к потере сознания. Бензол присутствует в ароматических нафтах, и его воздействие должно быть ограничено. Верхний погон дегексанизатора может содержать большое количество нормального гексана, который может воздействовать на нервную систему.
Хлористый водород может присутствовать в теплообменнике предварительного теплообменника, в верхней части градирни и в верхнем погоне. Сточные воды могут содержать водорастворимые сульфиды в высоких концентрациях и другие водорастворимые соединения, такие как аммиак, хлориды, фенол и меркаптан, в зависимости от сырого сырья и химикатов для обработки. Процессы конверсии, такие как крекинг, объединение и перегруппировка, изменяют размер и структуру молекул углеводородов, чтобы превратить фракции в более желательные продукты.
Ряд молекул углеводородов, обычно не встречающихся в сырой нефти, но важных для процесса очистки, образуются в результате конверсии. Олефины алкены, диолефины и алкины представляют собой ненасыщенные углеводородные молекулы цепного или кольцевого типа с по крайней мере одной двойной связью. Обычно они образуются в результате термического и каталитического крекинга и редко встречаются в природе в необработанной сырой нефти.
Простейшей молекулой алкена является моноолефин этилена с двумя атомами углерода, соединенными двойной связью, и четырьмя атомами водорода. Диолефины содержащие две двойные связи , такие как 1,2-бутадиен и 1,3-бутадиен, и алкины содержащие тройную связь , такие как ацетилен, встречаются в C 5 и более легкие фракции от крекинга. Олефины более реакционноспособны, чем парафины или нафтены, и легко соединяются с другими элементами, такими как водород, хлор и бром. После перегонки используются последующие процессы переработки для изменения молекулярной структуры фракций для создания более желаемых продуктов.
Один из этих процессов, крекинг, расщепляет или расщепляет более тяжелые нефтяные фракции с более высокой температурой кипения на более ценные продукты, такие как газообразные углеводороды, бензиновые смеси, газойль и мазут. В ходе этого процесса некоторые молекулы объединяются полимеризуются с образованием более крупных молекул.
Основными видами крекинга являются термический крекинг, каталитический крекинг и гидрокрекинг. В процессах термического крекинга, разработанных в г. Этот ранний метод, который производил большое количество твердого нежелательного кокса, превратился в современные процессы термического крекинга, включая висбрекинг, паровой крекинг и коксование.
Висбрекинг представляет собой мягкую форму термического крекинга, которая снижает температуру застывания парафинистых остатков и значительно снижает вязкость сырья, не влияя на диапазон его температур кипения. Остаток из колонны атмосферной перегонки подвергают мягкому крекингу в нагревателе при атмосферном давлении. Затем его гасят холодным газойлем для контроля над крекингом и подвергают мгновенному испарению в дистилляционной колонне.
Остаточная смола после термического крекинга, которая скапливается на дне колонны фракционирования, испаряется в вакууме в отпарной колонне, а дистиллят направляется на рецикл. При паровом крекинге олефины получают путем термического крекинга сырья с большими молекулами углеводородов при давлениях, немного превышающих атмосферное, и при очень высоких температурах.
Остаток парового крекинга смешивают с тяжелым топливом. Нафта, полученная в результате парового крекинга, обычно содержит бензол, который извлекают перед гидроочисткой. Коксование является тяжелой формой термического крекинга, используемой для получения прямогонного бензина лигроина коксования и различных фракций средних дистиллятов, используемых в качестве сырья для каталитического крекинга.
Этот процесс настолько полностью восстанавливает водород из молекулы углеводорода, что остаток представляет собой форму почти чистого углерода, называемую кокс. Двумя наиболее распространенными процессами коксования являются замедленное коксование и непрерывное контактное или жидкостное коксование, которые, в зависимости от механизма реакции, времени, температуры и исходного сырья, дают три типа кокса: губчатый, сотовый и игольчатый кокс. При коксовании контроль температуры следует поддерживать в узком диапазоне, так как при высоких температурах образуется кокс, который слишком трудно вырезать из барабана.
И наоборот, слишком низкие температуры приведут к получению суспензии с высоким содержанием асфальта. Если температура коксования выйдет из-под контроля, может произойти экзотермическая реакция. Коррозии подвержены нижняя часть колонны, высокотемпературные теплообменники, топка и замачивание барабанов. Непрерывные термические изменения вызывают вздутие и растрескивание корпусов коксовых барабанов.
Впрыск воды или пара используется для предотвращения накопления кокса в трубах печи замедленного коксования. Вода должна быть полностью слита из коксовщика, чтобы не вызвать взрыв при перезарядке горячим коксом. В аварийных ситуациях необходимы альтернативные средства выхода с рабочей платформы на вершину коксовых камер.
Ожоги могут возникнуть при обращении с горячим коксом, от пара в случае утечки паропровода или от горячей воды, горячего кокса или горячего шлама, которые могут выбрасываться при открытии коксовых установок. Существует возможность воздействия ароматических нафт, содержащих бензол, сероводород и монооксид углерода, а также следовых количеств канцерогенных ПАУ, связанных с коксованием.
Сточные кислые воды могут быть сильно щелочными и содержать нефть, сульфиды, аммиак и фенол.
Когда кокс перемещается в виде суспензии, в замкнутых пространствах, таких как бункеры для хранения, может происходить истощение кислорода, поскольку влажный уголь поглощает кислород. Каталитический крекинг расщепляет сложные углеводороды на более простые молекулы, чтобы повысить качество и количество более легких и желательных продуктов и уменьшить количество остатков.
Тяжелые углеводороды подвергаются воздействию катализаторов при высокой температуре и низком давлении, которые способствуют химическим реакциям. Этот процесс изменяет молекулярную структуру, превращая тяжелое углеводородное сырье в более легкие фракции, такие как керосин, бензин, сжиженный нефтяной газ, печное топливо и нефтехимическое сырье см. Выбор катализатора зависит от сочетания максимально возможной реакционной способности и наилучшей стойкости к истиранию.
Катализаторы, используемые в установках крекинга нефтеперерабатывающих заводов, обычно представляют собой твердые материалы цеолит, гидросиликат алюминия, обработанная бентонитовая глина, фуллерова земля, боксит и алюмосиликат , которые находятся в форме порошков, шариков, гранул или формованных материалов, называемых экструдитами.
Процессы каталитического крекинга очень гибкие, а рабочие параметры можно регулировать в соответствии с изменяющимся спросом на продукцию. Три основных типа процессов каталитического крекинга:. Установки каталитического крекинга с псевдоожиженным слоем имеют секцию катализатора стояк, реактор и регенератор и секцию фракционирования, которые работают вместе как интегрированная технологическая установка.
В FCC используется тонкоизмельченный катализатор, взвешенный в парах масла или газа, который действует как жидкость.
Крекинг происходит в питательной трубе стояке , по которой смесь катализатора и углеводородов протекает через реактор. Процесс FCC смешивает предварительно нагретую углеводородную загрузку с горячим регенерированным катализатором, когда он поступает в стояк, ведущий в реактор. Загрузка соединяется с рециркулирующим маслом в стояке, испаряется и нагревается до температуры реактора с помощью горячего катализатора.
По мере продвижения смеси вверх по реактору происходит расщепление загрузки при низком давлении. Этот крекинг продолжается до тех пор, пока пары масла не отделятся от катализатора в циклонах реактора. Полученный поток продукта поступает в колонну, где он разделяется на фракции, при этом часть тяжелой нефти направляется обратно в стояк в качестве рециркулируемого масла.
Отработанный катализатор регенерируют для удаления кокса, который накапливается на катализаторе во время процесса. Отработанный катализатор проходит через отпарную колонну катализатора в регенератор, где смешивается с подогретым воздухом, сжигая большую часть коксовых отложений. Добавляется свежий катализатор, а изношенный катализатор удаляется для оптимизации процесса крекинга.
Каталитический крекинг с подвижным слоем аналогичен каталитическому крекингу с псевдоожиженным слоем; однако катализатор находится в форме гранул, а не мелкодисперсного порошка. Гранулы непрерывно перемещаются по конвейеру или пневматическим подъемным трубам в бункер для хранения в верхней части установки, а затем под действием силы тяжести стекают вниз через реактор в регенератор. Регенератор и бункер изолированы от реактора паровыми затворами. Продукт крекинга разделяется на рециркулирующий газ, нефть, очищенную нефть, дистиллят, лигроин и влажный газ.
При термокаталитическом крекинге предварительно нагретое сырье проходит самотеком через слой каталитического реактора. Пары отделяются от катализатора и направляются в ректификационную колонну. Отработанный катализатор регенерируется, охлаждается и рециркулируется, а дымовой газ после регенерации направляется в котел на оксиде углерода для рекуперации тепла.
Следует проводить регулярные отбор проб и тестирование потоков сырья, продуктов и рецикла, чтобы убедиться, что процесс крекинга работает должным образом и что в технологический поток не попали загрязняющие вещества. Коррозионные вещества или отложения в сырье могут загрязнять газовые компрессоры.
Коррозия возникает там, где присутствуют как жидкая, так и паровая фазы, а также в местах, подверженных локальному охлаждению, таких как сопла и опоры платформы. При обработке исходного сырья с высоким содержанием азота воздействие аммиака и цианида может привести к коррозии, растрескиванию или образованию водородных пузырей на оборудовании из углеродистой стали в системе верхнего погона FCC, что можно минимизировать промывкой водой или ингибиторами коррозии.
Промывка водой может использоваться для защиты конденсаторов верхнего погона в основной колонне, подверженных загрязнению гидросульфидом аммония. Критическое оборудование, включая насосы, компрессоры, печи и теплообменники, должно быть осмотрено. Проверки должны включать проверку утечек из-за эрозии или других неисправностей, таких как накопление катализатора на детандерах, закоксовывание верхних фидерных линий из-за остатков сырья и других необычных условий эксплуатации. Жидкие углеводороды в катализаторе или попадающие в поток нагретого воздуха для горения могут вызывать экзотермические реакции.
В некоторых процессах необходимо соблюдать осторожность, чтобы гарантировать отсутствие взрывоопасных концентраций пыли катализатора во время перезарядки или утилизации. При выгрузке закоксованного катализатора существует вероятность возгорания сульфида железа. Сульфид железа самовозгорается при контакте с воздухом, поэтому его необходимо смочить водой, чтобы он не стал источником воспламенения паров.
Существует возможность воздействия чрезвычайно горячих углеводородных жидкостей или паров во время отбора технологических проб или в случае утечки или выброса. В процессах крекинга, в которых используются никелевые катализаторы, может происходить непреднамеренное образование высокотоксичного карбонила никеля, что может привести к опасным воздействиям. Регенерация катализатора включает отгонку паром и удаление кокса, что приводит к потенциальному воздействию потоков жидких отходов, которые могут содержать различное количество кислой воды, углеводородов, фенола, аммиака, сероводорода, меркаптана и других материалов, в зависимости от исходного сырья, сырой нефти и процессов.
Безопасные методы работы и использование соответствующих средств индивидуальной защиты СИЗ необходимы при обращении с отработанным катализатором, перезарядке катализатора или в случае утечек или выбросов.
Гидрокрекинг представляет собой двухстадийный процесс, сочетающий каталитический крекинг и гидрирование, при котором дистиллятные фракции крекингятся в присутствии водорода и специальных катализаторов с получением более желаемых продуктов. Гидрокрекинг имеет преимущество перед каталитическим крекингом в том, что сырье с высоким содержанием серы можно перерабатывать без предварительной десульфурации.
При этом тяжелое ароматическое сырье превращается в более легкие продукты при очень высоких давлениях и достаточно высоких температурах. Когда исходное сырье имеет высокое содержание парафинов, водород предотвращает образование ПАУ, снижает образование смолы и предотвращает образование кокса на катализаторе.
Гидрокрекинг дает относительно большое количество изобутана для сырья для алкилирования, а также вызывает изомеризацию для регулирования температуры застывания и дымообразования, оба из которых важны для высококачественного реактивного топлива.
На первом этапе сырье смешивается с рециркулирующим водородом, нагревается и направляется в первичный реактор, где большое количество сырья превращается в средние дистилляты. Соединения серы и азота превращаются с помощью катализатора в реакторе первичной ступени в сероводород и аммиак. Остаток нагревается и направляется в сепаратор высокого давления, где газы, богатые водородом, удаляются и перерабатываются.
Оставшиеся углеводороды десорбируются или очищаются от сероводорода, аммиака и легких газов, которые собираются в аккумуляторе, где бензин отделяется от высокосернистого газа.
Отпаренные жидкие углеводороды из первого реактора смешиваются с водородом и направляются в реактор второй ступени, где они подвергаются крекингу с получением высококачественного бензина, реактивного топлива и дистиллятной смеси. Эти продукты проходят серию сепараторов высокого и низкого давления для удаления газов, которые перерабатываются.
Жидкие углеводороды стабилизируются, разделяются и отгоняются, при этом легкие продукты нафты из установки гидрокрекинга используются для смешивания бензина, а более тяжелые нафты рециркулируются или направляются в установку каталитического риформинга. Осмотр и испытание предохранительных устройств важны из-за очень высокого давления в этом процессе. Надлежащее управление технологическим процессом необходимо для защиты от закупоривания слоев реактора.
Из-за рабочих температур и присутствия водорода содержание сероводорода в сырье должно быть строго сведено к минимуму, чтобы уменьшить возможность сильной коррозии. Необходимо также учитывать коррозию влажным углекислым газом в зонах конденсации.
При переработке сырья с высоким содержанием азота аммиак и сероводород образуют гидросульфид аммония, который вызывает серьезную коррозию при температурах ниже точки росы по воде.
Гидросульфид аммония также присутствует при отпарке кислых вод. Поскольку установка гидрокрекинга работает при очень высоких давлениях и температурах, для предотвращения пожаров важно контролировать как утечки углеводородов, так и выбросы водорода.
Поскольку это закрытый процесс, воздействие минимально при нормальных условиях эксплуатации. Существует вероятность воздействия алифатической нафты, содержащей бензол, канцерогенные ПАУ, выбросы углеводородного газа и паров, газа с высоким содержанием водорода и сероводорода в результате утечек под высоким давлением. Во время регенерации и замены катализатора может выделяться большое количество монооксида углерода. Паровая отпарка и регенерация катализатора создают потоки отходов, содержащие кислую воду и аммиак.
При работе с отработанным катализатором необходимы безопасные методы работы и соответствующие средства индивидуальной защиты. В некоторых процессах необходимо следить за тем, чтобы во время перезарядки не образовывалась взрывоопасная концентрация каталитической пыли.

Выгрузка закоксованного катализатора требует особых мер предосторожности для предотвращения пожаров, вызванных сульфидом железа. Два сочетающихся процесса, полимеризация и алкилирование , используются для соединения небольших молекул с дефицитом водорода, называемых олефины, извлекаемый из термического и каталитического крекинга, чтобы создать более желательные запасы бензиновой смеси.
Полимеризация — это процесс объединения двух или более ненасыщенных органических молекул олефинов с образованием одной более тяжелой молекулы с теми же элементами в той же пропорции, что и исходная молекула. Он преобразует газообразные олефины, такие как этилен, пропилен и бутилен, преобразованные на установках термического и жидкостного крекинга, в более тяжелые, более сложные молекулы с более высоким октановым числом, включая нафту и нефтехимическое сырье.
Олефиновое сырье предварительно обрабатывают для удаления соединений серы и других нежелательных веществ, а затем пропускают через фосфорный катализатор, обычно твердый катализатор или жидкую фосфорную кислоту, где происходит экзотермическая полимерная реакция. Это требует использования охлаждающей воды и подачи холодного сырья в реактор для контроля температуры при различных давлениях.
Кислоту в жидкостях удаляют промывкой щелочью, жидкости фракционируют, а кислотный катализатор рециркулируют. Пар фракционируют для удаления бутанов и нейтрализуют для удаления следов кислоты. В случае контакта воды с фосфорной кислотой, например, во время промывки водой при остановах, произойдет сильная коррозия, ведущая к отказу оборудования.
Коррозия также может возникать в трубопроводных коллекторах, ребойлерах, теплообменниках и других местах, где может осаждаться кислота. Существует вероятность воздействия едкого наполнителя гидроксида натрия , фосфорной кислоты, используемой в процессе или вымываемой во время капитального ремонта, а также пыли катализатора.
В случае потери охлаждающей воды существует вероятность неконтролируемой экзотермической реакции. Алкилирование объединяет молекулы олефинов, полученных в результате каталитического крекинга, с молекулами изопарафинов, чтобы увеличить объем и октановое число бензиновых смесей.
Олефины реагируют с изопарафинами в присутствии высокоактивного катализатора, обычно серной или плавиковой кислоты или хлорида алюминия , с образованием парафиновой молекулы с длинной разветвленной цепью, называемой алкоксид изооктан с исключительными антидетонационными свойствами. Затем алкилат отделяют и фракционируют. Алкилирование серной кислотой.
В установках сернокислотного алкилирования каскадного типа сырье, включая пропилен, бутилен, амилен и свежий изобутан, поступает в реактор, где контактирует с сернокислотным катализатором. Реактор разделен на зоны, причем олефины подаются через распределители в каждую зону, а серная кислота и изобутаны перетекают через перегородки из зоны в зону.
Теплоту реакции отводят испарением изобутана. Газообразный изобутан удаляют из верхней части реактора, охлаждают и возвращают в цикл, при этом часть направляют в башню депропанизатора. Остаток из реактора отстаивают, а серную кислоту удаляют со дна емкости и рециркулируют.
Алкилирование плавиковой кислотой. Существует два типа процессов алкилирования плавиковой кислотой: Phillips и UOP. Углеводород из зоны отстаивания загружают в основную ректификационную колонну. Основные накладные расходы фракционирования идут на депропанизатор. Пропан со следовыми количествами фтористоводородной кислоты HF направляется в отпарную колонну HF, а затем подвергается каталитическому обесфториванию, обработке и отправке на хранение.
В процессе UOP используются два реактора с отдельными отстойниками. Половину высушенного сырья загружают в первый реактор вместе с рециклом и подпиточным изобутаном, а затем в его отстойник, где рециркулируют кислоту, а углеводород загружают во второй реактор.
Другая половина сырья направляется во второй реактор, при этом отстойная кислота рециркулируется, а углеводороды загружаются в основную ректификационную установку. Последующая обработка аналогична технологии Phillips в том, что головной погон из основного ректификационного агрегата направляется в депропанизатор, изобутан рециркулируется, а алкилат направляется в разделитель.
Серная кислота и фтористоводородная кислота являются опасными химическими веществами, поэтому необходимо соблюдать осторожность при доставке и разгрузке кислоты. Некоторая коррозия и загрязнение в сернокислотных установках возникают в результате разложения эфиров серной кислоты или при добавлении щелочи для нейтрализации.
Эти сложные эфиры можно удалить обработкой свежей кислотой и промывкой горячей водой. Сбои могут быть вызваны потерей охлаждающей воды, необходимой для поддержания температуры процесса. Давление на стороне охлаждающей воды и пара теплообменников должно поддерживаться ниже минимального давления на стороне кислотной среды, чтобы предотвратить загрязнение водой.
Вентиляционные отверстия могут быть направлены в скрубберы кальцинированной соды для нейтрализации газообразного фтористого водорода или паров плавиковой кислоты перед выбросом. Для локализации технологических установок могут быть предусмотрены бордюры, дренаж и изоляция, чтобы сточные воды можно было нейтрализовать перед выпуском в канализационную систему. Блоки плавиковой кислоты должны быть тщательно осушены и химически очищены перед капитальным ремонтом и входом, чтобы удалить все следы фтористого железа и плавиковой кислоты.
После останова, когда использовалась вода, агрегат следует тщательно высушить перед введением фтористоводородной кислоты. Утечки, разливы или выбросы плавиковой кислоты или углеводородов, содержащих плавиковую кислоту, чрезвычайно опасны. Необходимы меры предосторожности для обеспечения бережного обращения с оборудованием и материалами, контактировавшими с кислотой, и их тщательной очистки перед тем, как они покинут технологическую зону или нефтеперерабатывающий завод.